突破物理极限,迈向工艺巅峰!解析英特尔全新10nm工艺
半导体工艺是半导体技术发展的核心。英特尔作为全球最大的半导体企业,在半导体工艺方面一直保持着领先地位,并且引领了大量全新技术的发展。不过近几年,英特尔半导体工艺的发展速度似乎逐渐慢了下来,比如14nm工艺竟然用了三代,10nm工艺也被竞争对手抢先。这是英特尔技不如人还是另有隐情?同样都是10nm工艺,真的在性能、晶体管密度方面表现相当吗?请看本文为你带来的深入分析。
毫不夸张的说,英特尔的发展史,就是一部半导体技术和制造工艺的发展史。不过近年来随着三星、台积电等厂商的崛起,高通、英伟达等无晶圆厂商的存在,使得英特尔在半导体产业方面的话语权有所减弱。尤其是最近一段时间,三星和台积电在全新工艺方面积极投入,并且已经开始了10nm技术的使用。反观英特尔方面,其新处理器依旧采用14nm工艺,似乎让人们看到了一个步履蹒跚、缓步前行的巨无霸身影。那么,实际情况真的是这样吗?为了全面梳理英特尔在产业上的发展历史和优势技术,并展示自己强大的研发实力,2017年9月下旬,英特尔在北京召开了技术宣讲会,其中包含了大量英特尔在工艺上的突破和它在10nm工艺上的进展。
从摩尔定律说起
说起半导体技术的发展,人们最先想到的应该就是摩尔定律了。基本上任何一个关注制程的文章都要提及这个对半导体产业产生了重大影响的定律。英特尔创始人之一的戈登·摩尔曾说过:“当价格不变时,集成电路上可容纳的元器件的数目,约每隔18~24个月便会增加一倍,性能也将提升一倍。”
摩尔定律在1975年,距今已经过去了32年。在这32年内,产业界的发展脉络基本上都是遵循着摩尔定律。摩尔定律的重要性在于,它并不是一个被人们发现的物理或者数学定律,而是一个由经验和市场、产业技术发展角度所推导出来的“经验定律”。令人惊讶的是,这个定律竟然精确的运行了30年之久。1971年的4004处理器内平均包含约2300个晶体管,到1997年奔腾Ⅱ这一数据变为750万个晶体管,在26年间增加了约3200倍,和摩尔定律基本相符。
▲摩尔定律在从很长一段时间内都持续发挥着作用。英特尔展示了从130nm到7nm发展历程中对摩尔定律的坚持。
从英特尔提供的一张图片上,可以看到摩尔定律的有效性,它通过利用每平方毫米晶体管数量的增加乘以每平方毫米芯片价格的增加,来证明每平方毫米单位价格晶体管的数量是符合摩尔定律的。通过这张对比图我们可以看到,在英特尔14nm工艺之前,每平方毫米晶体管数量的提升幅度是符合回归曲线的,但是从14nm开始到10nm、7nm,晶体管的密度大幅度提升,从而开始偏离回归曲线。与此相对应的是晶体管每平方毫米的价格在逐渐上涨,但是两者相乘后每平方毫米每单位晶体管的价格反而逐渐下降,依旧符合摩尔定律。
▲英特尔给出的PC处理器上每晶体管加权平均成本的数值,可见是持续降低的。
为什么10nm和7nm的数据会偏离回归曲线?在这一点上,英特尔没有避讳,直接提出了一项全新的技术:超微缩技术。这项全新的技术(或者多项技术综合)带来了除节点更替之外更新一轮的芯片面积和晶体管体积的缩小,其效果甚至不亚于节点技术的跨越。这被英特尔称为“节点内优化”。这也解释了为什么最近数年来我们看到英特尔的产品总是比较长的停留在一个节点时间上,其技术本质和我们多次提到的不能单纯用节点代次来考量晶体管的制造能力一样。毕竟芯片制造中节点只是一个方面,还有更多的方面影响着晶体管的制造、性能和成本。接下来我们还将会更多地为大家展示这些内容。
▲借助“超微缩技术”,英特尔实现了节点间工艺的进步,这在10nm和14nm工艺上显示的尤为明显。
英特尔的超微缩技术突破了传统芯片面积每代缩小0.62倍的极限,在10nm和14nm的芯片上带来了超过0.5倍的面积缩小,分别为0.46和0.43倍。如果你对这个数据没有概念的话,英特尔给出的另一个数据证明了这一点:在45nm技术下100平方毫米的芯片,在32nm技术可以缩小为62平方毫米,在22nm技术下进一步缩小至38.4平方毫米,14nm和10nm下这个数据分别是17.7平方毫米和7.6平方毫米。如果我们只关注10nm的话,相比22nm,10nm的芯片面积只有22nm芯片的19.7%,也就是只有22nm的1/5大小,尺寸缩减幅度惊人。
芯片尺寸缩减幅度变大的另一个好处就是成本的降低。对于芯片制造业而言,芯片面积是决定成本非常重要的因素,在一张晶圆上切割出来的芯片数量越多,那么相应的成本就会越低。对英特尔来说,成本的降低意味着毛利率的增加和经营情况的持续改善。英特尔也使用数据证明了由于晶体管数量降低而带来的收益增加,以及不断提升的毛利率水平。
密度100MTr/平方毫米,英特尔10nm技术初现
在正式介绍英特尔的10nm技术之前,我们先来看一些知识。
衡量一种制造技术的优劣,除了我们常见的频率、电压、漏电电流控制等内容,其核心的数据依旧是晶体管密度。就像上文所说,晶体管的密度决定了制造的成本,而制造的成本又和企业的运营状况息息相关。从另一个角度来说,晶体管制造技术不断挑战的就是制造的密度,制造密度上升是很多问题得到解决的象征,因为一旦有各种各样的因素阻碍或者技术难点无法完成,制造密度就很难得到实质性的上升。
由于晶体管制造的复杂性,单纯的利用代次来衡量工艺水平是不完全准确的。不光每代晶体管工艺中有面向不同用途的制造技术版本,不同厂商的代次之间统计算法也完全不同。为了解决这个问题,目前业内常用的衡量晶体管工艺密度的公式是“栅极间距×单元高度”。无论如何在商业上改变代次的宣传等内容,晶体管的栅极间距和逻辑单元高度是不会说假话的。通过这个公式来计算的话,英特尔传统的逻辑单元面积平均每代缩小0.49倍,但是在10nm工艺和14nm工艺上,每代缩小倍数高达0.37倍。
▲英特尔工艺在14nm上的进展,带来了相当与前代产品0.37倍的单元面积。
但是,利用这个公式来衡量晶体管工艺的水平,也存在一定问题,主要是目前一颗芯片中不同的单元对工艺要求是不同的,比如SRMA和逻辑单元,在制造上就存在一定的差异。传统中人们往往以厂商生产SRMA开始作为工艺成熟的标志,并通过考察SRMA的体积和密度来衡量半导体工艺的水平,这种考察有一定代表意义,但不够全面。鉴于此,业内一些专家又提出了一种全新的工艺衡量计算方法,包含了NAND和复杂的扫描触发器逻辑单元,并分别给予0.6和0.4的加权值,通过统计数量和面积的关系,用于计算最终晶体管数量的加权平均值。
根据新的工艺计算方法,英特尔给出了一张逻辑晶体管密度的表格。在45nm工艺下,晶体管密度大约在每平方毫米330万个,随后32nm上升至大约每平方毫米750万个,22nm上升至每平方毫米1530万个以上,上升倍数大约为2.1倍。但是到了14nm,它大约上升到3750万个左右,大幅度提示2.5倍。10nm更是惊人地上升至一亿个每平方毫米,相比14nm再度跃升了2.7倍之多。综合来看,英特尔在晶体密度上大约每两年翻一番,基本上达到了摩尔定律的要求。
▲英特尔数代工艺逻辑面积降低比率。
▲在全新的计算方法下,英特尔晶体管密度提升的数据。
▲英特尔每平方毫米晶体管密度突破一亿。
在这里,我们依旧尤为关注英特尔在14nm和10nm技术上的进展。尤其是超微缩技术带来密度大幅度上升。有关这部分内容,英特尔给出了一些数据和技术细节来展示超微缩技术对晶体管全面的缩小能力。
从数据上可以看到,相对22nm而言,14nm的鳍片间距、互联间距、单元高度和栅极间距分别是前代产品的0.7倍、0.65倍、0.48倍和0.78倍,综合起来就是相当与前代产品0.37倍的单元面积。在10nm上,这种缩减还在继续。其中10nm相对14nm,除了鳍片间距、最小金属间距、单元高度和栅极间距缩减至之前的0.81倍、0.69倍、0.68倍和0.78倍外,10nm的虚拟栅极从14nm的2个降低至1个,栅极出点形式也从传统的标准形式改变成了更为节省面积的COAG上覆盖形式,这带来了晶体管密度2.7倍的提升。
为了进一步清晰展示10nm和14nm的工艺优势,英特尔还展示了部分技术的改进,解释如下:
首先是第三代FinFET晶体管。FinFET也就是鳍式场效应晶体管,最早在22nm技术上被英特尔采用,这项技术的特点在于将传统平面、越来越薄的绝缘层改变为立体的状态,通过大幅度提升源极和栅极的接触面积,使得晶体管在控制漏电电流方面得到改善。一般来说,FinFET的鳍片高度在很大程度上决定了其接触面积和对漏电电流的控制能力。英特尔的数据显示,10nm的鳍片相对高度更高,相比14nm高度提升了25%,同时间距缩小了25%,性能得以显著提升。
▲第三代FinFET技术,鳍片变得更高,栅极距离变得更窄。
▲单个虚拟栅极进一步降低了芯片面积。
▲英特尔新的22nmFFL工艺在漏电电流控制、低功耗方面表现卓著。
▲22nmFFL工艺的驱动电流甚至达到了14nm++工艺的水平。
▲英特尔22nmFFL的漏电电流甚至相比传统水平最多降低了500倍。
第二项技术是COAG,全称是Contact Over Active Gate。传统的触点位于栅极一侧,这占用了不少的面积同时影响了晶体管的体积。但是新的COAG技术将触点上移到了栅极上方,不再占用额外的栅极面积,带来了晶体管面积大约10%的缩小。
第三项技术是单个虚拟栅极。之前14nm技术需要多个虚拟栅极存在,这些虚拟栅极存在的原因是在较小的晶体管并联时,加入虚拟栅极能够更为精确的匹配电流。之前英特尔在活跃栅极附近会匹配超过一个虚拟栅极,但是在10nm工艺上,由于工艺进步,英特尔可以再单元边界使用单个虚拟栅极就完成匹配电流的工作。实际上根据图形来看,之前每个晶体管需要2个虚拟栅极,左右各一,用于隔开活跃栅极,但是目前英特尔可以做到两个晶体管中间只插入一个虚拟栅极,进一步降低了面积浪费,提高了密度。
▲英特尔在10nm工艺上的创新,注意10nm工艺采用了新的四重曝光技术。
最后是库文件的更新。在10nm上,英特尔采用了新的库文件,单元高度从之前14nm的399纳米提升至10nm的272纳米,缩减至前代的0.68倍,于此相应的栅极间距也有缩减,进一步缩减了每个单元的面积。
▲全新的库文件,针对10nm设计。
英特尔在超微缩技术方面只介绍了上述四个比较典型的技术内容。考虑到半导体制造工艺的复杂性,英特尔肯定还有其他尚未说明的技术依旧处于保密状态,但是仅仅就目前披露的内容来看,10nm和14nm上英特尔的创新能力依旧令人惊讶,这不单是芯片在制程节点上的自然进化,还包含了大量节点内创新技术的使用。这些技术的综合应用,才带来了10nm工艺2.7倍密度提高、每平方毫米一亿晶体管的壮举。
除了10nm工艺外,英特尔还简单提到了22nmFFL工艺。这是英特尔为代工业务推出的全新工艺,其主要客户群体瞄准的是移动、低功耗芯片等对功耗、尺寸和散热非常敏感的产品。根据英特尔的介绍,22nmFFL工艺结合了英特尔FinFET和其他低漏电技术,使得晶体管漏电率降低了100多倍,驱动电流甚至达到了14nm工艺的水平,堪称业界最出色的超低功耗先进工艺。
领先整整一代,英特尔工艺对比三星和TSMC
英特尔全新的10nm和22nmFFL与业内其他厂商尤其是三星和TSMC的技术水平对比,又是一种怎样的结果呢?这一次英特尔非常自信地给出了三家厂商10nm工艺的部分参数,并给予了详细对比。
从英特尔给出的数据可以看出,在10nm工艺上,英特尔逻辑晶体管密度可达1亿每平方毫米,对比TSMC只有4800万每平方毫米,三星也只有5160万每平方毫米,英特尔几乎以碾压的态势赢得了胜利。其中差距最大的是栅极间距和逻辑单元高度,英特尔几乎领先20%和30%,其他的鳍片间距、最小金属间距等也有非常显著的优势。
▲晶体管工艺的进步还带来了每瓦特性能的提升。
除了本代10nm技术外,英特尔还在规划10nm+和10nm++两代工艺,其中10nm++技术预计会在2019~2020年左右推出,相比目前的技术无论是性能、功耗还是每瓦特性能比都会得到持续的提升。根据英特尔数据,目前英特尔的10nm工艺在综合性能上比三星和TSMC的工艺大约领先20%,10nm++工艺甚至会带来30%以上的提升,也就是说即使都是10nm工艺,其技术差别带来的性能和密度差距,甚至不比晶体管制造工艺代差小。
▲英特尔多代次工艺的晶体管密度和台积电、三星的工艺对比,其中10nm工艺最为出色。
▲SRAM制造显示英特尔10nm工艺相对14nm工艺面积缩小了40%。
▲英特尔10nm工艺相比台积电和三星有大约20%~30%的提升。
除了10nm工艺外,英特尔用自家的其他工艺对比了22nmFFL工艺。简单来说,22nmFFL工艺在一些关键性能上已经非常接近14nm工艺,尺寸上比传统22nm工艺领先太多。如果英特尔在价格、代工产业链上有所作为的话,这将是一个非常有竞争力的生产技术。
▲英特尔还在规划10nm+和10nm++工艺,预计2019~2020年推出。
总的来看,英特尔在半导体制造上的技术依旧保持了领先地位,其10nm工艺无论是密度、电流、电压还是性能功耗比等各个方面,都远超同代次其他厂商的工艺。不仅如此,在晶体管密度方面,英特尔一亿晶体管每平方毫米的优势,使得三星和TSMC即使在应用了7nm工艺之后也可能很难超越。
作为这个星球上最高端、最精密同时又是最廉价(每晶体管价格)的生产方式,英特尔在半导体制造上每走一步,都代表了人类又向前迈进了一步。我们也希望英特尔和其他企业携起手来,在未来的半导体产业上继续努力,继续遵循着摩尔定律的脚步,将人类的计算能力和制造能力推向一个全新的高峰。
关注公众号:拾黑(shiheibook)了解更多
[广告]赞助链接:
四季很好,只要有你,文娱排行榜:https://www.yaopaiming.com/
让资讯触达的更精准有趣:https://www.0xu.cn/
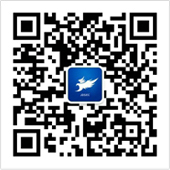
随时掌握互联网精彩
- 1 总书记的一周 4990544
- 2 微信转账520和1314能要回吗 4936913
- 3 伊朗总统遗体已被送往公墓 4811482
- 4 数据彰显经济运行强劲脉动 4795952
- 5 专家称十年后房子不可能卖白菜价 4637394
- 6 外交部:台湾是中国一省 没独立地位 4520319
- 7 吴艳妮登上英国报纸:被赞迷人 4469755
- 8 #狐妖小红娘月红篇# 4323582
- 9 新疆辟谣楼兰故城门票3500元 4291680
- 10 520垃圾桶变花桶 4149280